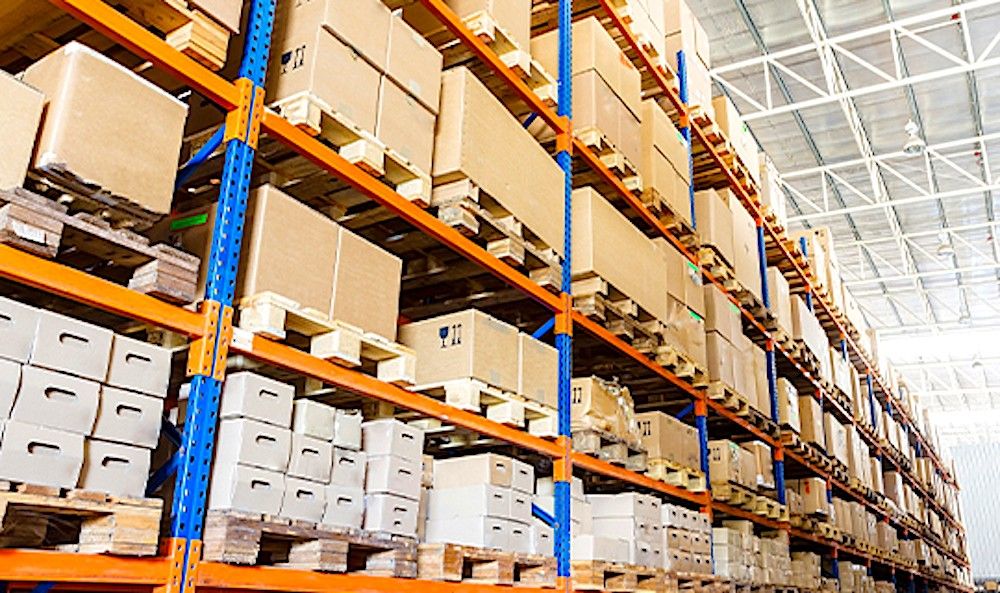
Tras una investigación de tres años y una inversión de 2.170.500,66 euros, el consorcio de empresas vascas del proyecto Nondago ha desarrollado y validado ocho herramientas que podrán implementarse en plantas de producción, y permitirán optimizar el seguimiento en tiempo real de todos los elementos en movimiento, incluso en entornos hostiles.
Las herramientas permitirán mejorar la seguridad de operaciones, la productividad y la logística en planta, contribuyendo al incremento de un 8% en la productividad de procesos logísticos, y la reducción en un 12% de los recorridos de los puentes grúa y en un 10% de los movimientos de las carretillas elevadoras. Esto supone un ahorro de los costes de producción y una mejora en la competitividad de las empresas.
El proyecto, que ha contado con la financiación del ‘Programa Hazitek 2021', ha combinado el diseño de nuevos dispositivos de posicionamiento capaces de operar en entornos hostiles, haciendo uso de tecnologías UWB, Bluetooth 5.1 AoA o láser, junto con el desarrollo de soluciones de analítica avanzada de datos y software de gestión para la visualización y toma de decisiones.
En este sentido, se han desarrollado y optimizado hasta ocho nuevos conocimientos, que se han validado en casos concretos como el seguimiento de los movimientos de puentes grúa, de carretillas elevadoras o de brazos robóticos, cambios de molde y utillaje, así como la monitorización de personas en espacios confinados.
Así, con el apoyo de la analítica de datos y de software de gestión, se han logrado optimizar los movimientos en planta y enviar alertas para mejorar la seguridad de las operaciones, así como reducir tiempos y costes de producción.
A lo largo del proyecto, se ha trabajado en sistemas de posicionamiento de bajo consumo, que ofrezcan datos fiables tanto en interiores como en exteriores, nuevos algoritmos en entornos complicados y herramientas que simplifiquen la configuración remota.
La validación de estos dispositivos y herramientas permitirá lograr unos procesos más eficientes y flexibles, con mejoras en la seguridad y en la automatización de las operaciones, así como mejoras en los productos desarrollados, y una reducción en el uso de los recursos y en el impacto ambiental.
Para conseguirlo, el proyecto ha validado las herramientas en situaciones reales como la monitorización y automatización de puentes grúa y de carretillas elevadoras, o la implementación de sistemas de seguridad para robótica colaborativa.
Las herramientas se han validado también en un sistema de seguridad de las personas en espacios confinados, mejorando el control de la ubicación y reduciendo los tiempos de respuesta en caso de ser necesaria la evacuación y atención del operario que deba realizar tareas de limpieza en el interior de tanques industriales.
En el proyecto, se ha apostado por tecnologías de Radiofrecuencia y 'Ultra Wideband', para lograr así el objetivo científico técnico de una precisión de 20 centímetros que facilite el despliegue de tecnologías de posicionamiento en entornos industriales.