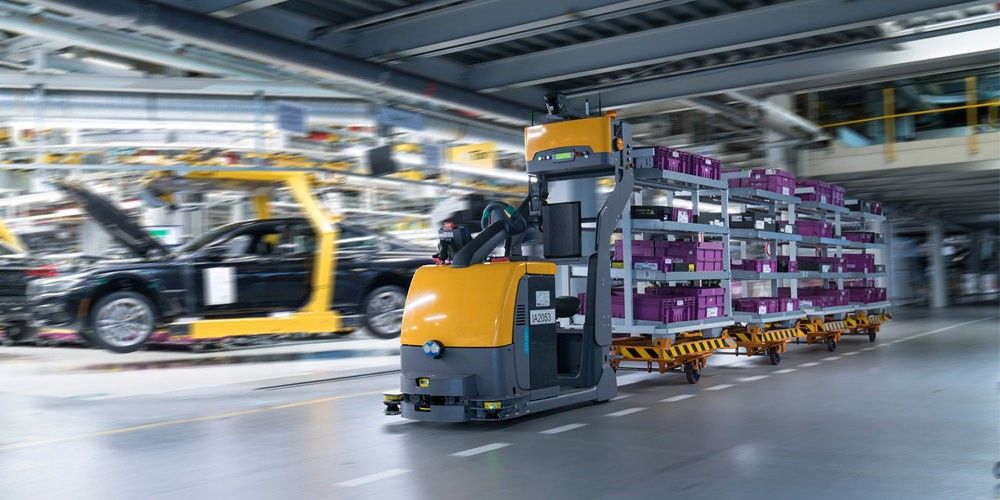
La llegada de la digitalización, la robótica y la industria 4.0 al sector de la automoción ha revolucionado el trabajo diario en los almacenes, que han logrado automatizar diferentes tareas, sustituyendo a los operarios de los trabajos más pesados y mejorando la competitividad de las plantas.
Los robots móviles autónomos, o AMRs, se adaptan fácilmente a los procesos de producción y permiten gestionar de forma más eficiente los recursos y la comunicación entre las distintas áreas de la empresa. Son un claro ejemplo de cómo los robots pueden colaborar con los empleados para simplificar su trabajo, dicen desde Seat, que ha incorporado en 2021 los EffiBOT de Effidence en su planta de Martorell, Barcelona.
Se trata de una solución fácilmente escalable. En el caso del fabricante, ha incorporado dos en fase experimental, pero no descarta ampliar esta cantidad, pues el sistema ayuda a los empleados a evitar las cargas pesadas, pudiendo transportar hasta 250 kg en carga y 500 kg en arrastre.
La diferencia con un Vehículo de Guiado Automático, AGV, es que pueden reconocer su entorno y establecer su propia ruta, esquivando los obstáculos que encuentren en su camino.
La planta de Martorell cuenta también con unos 20 robots colaborativos, conocidos como cobots, que utiliza para colocar el ‘lettering’ a los modelos Ibiza y Arona.
[sumario]El Big Data permite emitir alertas para prevenir las averías en las diferentes áreas de las plantas de automoción”.[/sumario]
Estos robots, que se caracterizan por su flexibilidad y su capacidad para colaborar activamente con los humanos, pueden marcar la diferencia en la cadena logística del sector de la automoción. Son fácilmente configurables, con plazos de amortización muy ajustados y permiten reducir los tiempos de producción o sustituir a los operarios en trabajos peligrosos o pesados.
La versatilidad de los ‘cobots’
PSA también los utiliza en su planta de Vigo para la fabricación del Citroën Berlingo o el Peugeot Partner, lo que le ha llevado a aumentar sustancialmente su eficiencia y productividad. Se utilizan para tareas como el control de calidad, o el atornillado o apilado de piezas.
A ello se añade el uso del Big Data para mejorar la eficiencia de los trabajos en el área de pintura a partir de un software que recoge datos como la temperatura de la cabina, atmósfera, humedad o datos de la propia pintura, para cruzarlos con los resultados de calidad de cada carrocería. El análisis de estos datos con Inteligencia Artificialpermite identificar problemas y establecer los parámetros ideales del proceso productivo.
También están en la planta de Opel en Figueruelas, que ha automatizado el proceso de sellado de las partes móviles en las carrocerías de los vehículos con robots que utilizan cámaras de visión artificial para una mayor precisión.
En su camino por adaptarse a la revolución del vehículo autónomo y conectado, Renault automatiza una parte de su producción en sus plantas españolas gracias a los robots colaborativos, apostando al mismo tiempo por la conexión de todas las instalaciones entre sí, que combinado con AGVs, permite a los operarios concentrarse en tareas de mayor valor añadido, agilizando todo el tráfico en las instalaciones.
A su vez, Volkswagen Navarra incorporó en 2020 un cobot en su planta de producción para ayudar en el montaje del Polo y el T-Cross. Se encarga de la aplicación de la masilla del alerón del coche, lo que supone una mejora en la calidad del acabado, ya que siempre aplica la misma cantidad de producto y lo hace en el lugar exacto.
Los exoesqueletos pueden ayudar a evitar muchos problemas relacionados con la salud laboral de los empleados.
La actividad en esta planta con un alto grado de automatización,utiliza robots para trabajos como la aplicación de adhesivo de las lunas en la nave de montaje. En la sección de chapistería, de hecho, se utilizan más de 700 robots, que realizan aproximadamente el 95% del trabajo. También ha incorporado en 2020 cuatro AGVs, para el suministro en línea de montaje de los laterales de los vehículos para su posterior unión al resto de la carrocería.
El sistema está perfectamente sincronizado con el sistema robótico de la línea de montaje. De este modo, una vez que el contenedor con los laterales de chapa ha quedado vacío, el vehículo autónomo recibe una señal para retirarlo y dejarlo al margen. A continuación, el vehículo recoge otro contenedor lleno y lo traslada hasta el punto de la línea donde debe realizarse el suministro al sistema robótico, que posteriormente efectuará los procesos de soldadura para unir piezas de menor tamaño al conjunto del lateral.
Otro ejemplo es el de Ford, que utiliza robots colaborativos en su planta de Colonia para aplicar los toques finales a los vehículos en las líneas de producción, lijando de forma muy fina toda la superficie. En 2020 inició un piloto en USA para la introducción de robots cuadrúpedos equipados con cámaras, que se utilizan para escanear las instalaciones y ayudar a los ingenieros en la actualización del diseño.
[sumario]Mercedes-Benz cuenta con el primer robot colaborativo capaz de trabajar con vehículos en movimiento, instalado en su planta de Vitoria”.[/sumario]
No obstante, no ha renunciado al uso de los AGVs, pues en 2021 ha iniciado un proyecto en Almussafes que permitirá la gestión de una pequeña flotade estos vehículos con navegación simultánea de localización y mapeo, para ser utilizados en interiores y exteriores. Además contribuirá al control de las AGV mediante gestos, sin utilizar ningún tipo de equipo especial, como guantes hápticos o gafas de realidad aumentada. Mediante una experiencia de inmersión de realidad virtual, el operario obtendrá una visión interactiva de alta calidad de lo que ocurre en cada AGV.
El fabricante también utiliza el Big Data para que los ingenieros reciban alertas de fallos. De hecho, ha recibido el premio ‘Factories of the Future Awards 2021’ por su modelo de predicción de averías en el área de estampación, consistente en la obtención de la mayor cantidad de datos posibleque procesados con herramientas relacionadas con la Industria 4.0. y IA, establecen posibles indicadores de predicción.
Asimismo, ha introducido un robot autopropulsado de reparto autónomoque lleva piezas de repuesto a la línea de producción, empleando para ello la tecnología de detección LIDAR.
Exoesqueletos para la salud laboral
Siguiendo con la idea de reducir los esfuerzos de los empleados, es importante señalar las ventajas de los exoesqueletos, que pueden evitar muchos problemas relacionados con la salud laboral, al evitar daños musculares en las tareas diarias. Los que utiliza Ford en Almussafes han sido desarrollados con titanio y fibra de carbono, y ayudan al operario cuando está de pie o en una postura forzada a levantar, mover o cargar cualquier pieza de más de tres kilos.
Igualmente, PSA lleva cuatro años realizando pruebas con exoesqueletos en Vigo, desarrollados en el Centro Tecnológico de Automoción de Galicia, para evitar las lesiones que suelen producirse en los trabajos muy repetitivos, mejorando la ergonomía en diferentes puestos de la planta.
Ford utiliza un robot autopropulsado en su planta de Almussafes para el traslado de piezas.
También Nissan incorporó en 2018 esta tecnología en su planta de la Zona Franca de Barcelona, y según su experiencia, su utilización podía llegar areducir hasta en un 60% el esfuerzo en determinados músculos. En esta misma instalación, se incorporó un sistema de impresión 3D para crear herramientas, plantillas y accesorios para la línea de producción, reduciendo el tiempo de diseño, perfeccionamiento y fabricación de una semana a un día.
Seat es otro de los fabricantes que ha apostado fuerte por la impresión 3D con su 3D Printing LAB es Seat, que en su planta de Martorell utiliza esta tecnología para imprimir piezas en un tiempo aproximado de 15 horas. Esto permite hacer varias versiones en una misma semana, que se pueden probar y volver a modificar para ir mejorándolas.
El 80% de las piezas que se imprimen son prototipos para el desarrollo de vehículos, pero también se fabrican herramientas a medida para la línea de montaje, logos personalizados e incluso salvamascarillas y tiradores de puerta para ayudar en la prevención del coronavirus.
Mercedes-Benz cuenta desde 2021 en su planta de Vitoria con el primer robot colaborativo que trabaja con vehículos en movimiento, desarrollado a través de la Universidad del País Vasco, que facilita el avance de las tareas en la línea de montaje. Es capaz de ir corrigiendo el movimiento de la plataforma móvil para seguirla y, a su vez, realizar pequeñas correcciones de posicionamiento hasta completar el trabajo.
El fabricante, acaba de instalar robots móviles en su planta turca de camiones de Aksaray, para los procesos de soldadura y la colocación de parabrisas. Además, el Grupo Daimler ha desarrollado el ecosistema digital MO360, que comprende distintas aplicaciones de software , e integra la información de los procesos de producción y los sistemas IT de más de 30 plantas de fabricación, facilitando el acceso a datos e instrucciones de trabajo a los empleados.
A la vista está que el futuro de la automoción, sea cual sea el fabricante, pasa por la digitalización, y especialmente la automatización y la robotización, procesos que se están desarrollando con mucha rapidez y para los que se espera un fuerte impulso en la próxima década.